Nere (sub-brand of Strand), an Australian household name known as the destination store for luggage, approached BLOND to design a new lightweight luggage line. The brief was to design a suitcase family made from injection moulded Polypropylene (PP) plastic, which provided an opportunity to explore high-fidelity surface detailing and textures—helping to differentiate from the more common vacuum-formed luggage shells. BLOND harnessed the capabilities of this manufacturing process to not only increase structural integrity and reduce weight, but also maximise brand exposure through a sweeping pattern that frames the strategically positioned logos.
Standing out in a saturated market is extremely difficult. Our initial strategic research and analysis into the current market landscape helped us to identify that hard shell suitcases share a common problem—cracking in transit due to a lack of structural integrity. BLOND addressed this by applying a scalloped pattern across the entire suitcase, made possible by using injection moulded recyclable PP. This provided the opportunity to explore high-fidelity surface detailing and textures; an advantage of the injection moulding manufacturing process over the more commonplace vacuum-formed luggage shells. The pattern acts as a set of external ribs that strengthen the shell, and enable a reduced wall thickness—making for a suitcase that isn’t only stronger, but lighter. The scalloped pattern also serves a second purpose of creating visual intrigue, through the application of high-fidelity gloss and matte surface treatments, only achievable through injection moulding. This eye-catching pattern emanates from the Nere logos—positioned purposefully on opposing top corners of the suitcase, increasing visibility as the suitcase is being pushed along by the user, further enhancing brand exposure.
Services:
Design Strategy
Industrial Design
Product Design
Design for Manufacture (DFM)
Manufacture Support
Visualisation
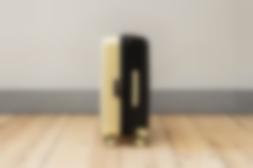
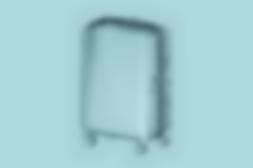
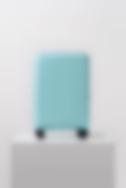
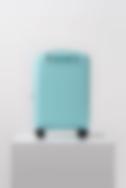
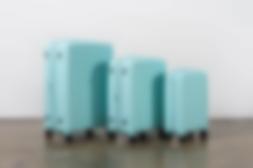
Injection moulded PP suitcases are much lighter than their vacuum-formed ABS and PC (Polycarbonate) counterparts—but it is challenging to mould large parts that are typically vacuum-formed without deformations and surface warping. Achieving a lightweight yet strong PP injection moulded suitcase is made possible firstly by the properties of PP, which, when compared to ABS and PC, is more flexible and less prone to cracking. Secondly, the unique surface pattern is strategically designed for injection moulding, allowing us to reduce wall thicknesses while strengthening the suitcase’s shell. This in turn uses much less plastic than vacuum formed cases, making it not only lighter and stronger, but also better for the environment. Ensuring structural integrity was key to promoting longevity; with cracking during transit being one of the most common failures of hard shell suitcases. The pattern therefore acts as a set of external ribs that strengthen the shell, while enabling a reduced wall thickness. As a result, the increased durability and lighter weight of the suitcase reduces carbon footprint for both users and airlines when travelling.
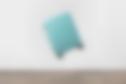
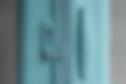
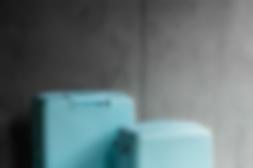
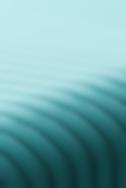
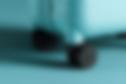
Most commercial suitcases position their logo centrally to the front face—this is often blocked by the user walking beside them or is too low down to be visible to others. To address this observation, the Nere logo badges uniquely occupy the two opposing top corners, which allows the logo to be seen from a wider range of viewpoints. Consideration was also made to the shaping and positioning of components, such as the wheel housings and Nere badges—to ensure they did not interrupt the sweeping pattern. Additionally, custom TSA locks mimic the soft edges of the suitcase detailing.
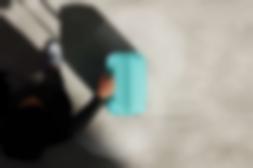
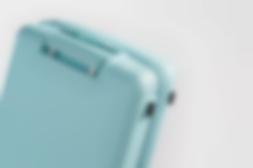
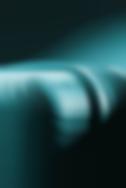
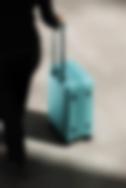
With the climate and environment in mind, material sourcing for the internals was also highly considered throughout the design development—each suitcase liner is made from 100% recycled lining, helping to maximise reuse and reduce waste.
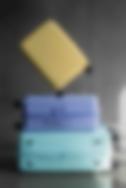
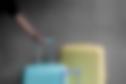
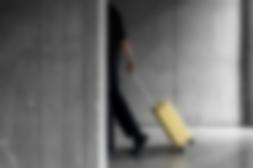
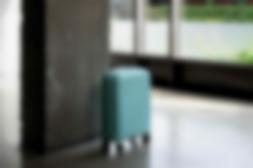
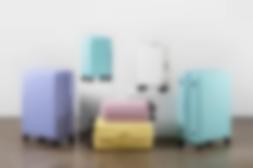